You’ll be glad you crunched the numbers.
Because calculating the Total Cost of Ownership (TCO) of the ERP systems you’re eying will do the following for you:
- Define the company-wide impact of the project
- Attach a number to the capital and resource investment you need to plan for
- Identify progress toward your ERP ROI.
With a TCO number in hand, you’ll also see more clearly what ERP system will best meet your needs.
So, where do you start?
This post describes the journey of this critical calculation.
What is the Total Cost of Ownership equation?
From a big-picture point-of-view, the TCO equation is simple:
TCO = Purchase price + cost of operations over the software’s lifespan.
What costs should you include in the Total Cost of Ownership?
TCO costs can be divided into the following four categories:
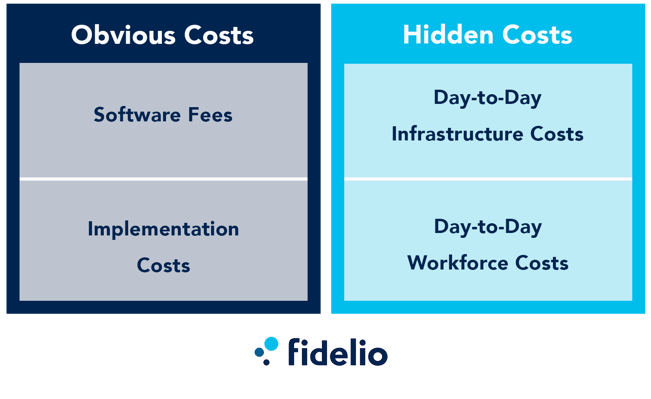
Although the basic TCO equation is simple, and the categories you need to cover are clear, it’s when you get into the details that your fellow executives need to agree on where to draw the line.
For example, are you going to include the costs of unfortunate events, like malware or virus attacks and stolen information? What about the cost of insurance against such events? Do you estimate a cost for damage to reputation?
Below, we discuss the components of each of our four cost categories.
What are ERP software fees? On-premise vs. cloud-based
On-premise ERP software
The first ERP systems developed were on-premise solutions for large enterprises. Before installing such a system, a company had to buy, at considerable cost, servers and backup servers (for redundancy) as well as licenses to run this software.
These large enterprises had an IT staff that could install, maintain, troubleshoot, develop, upgrade, and secure the ERP software while also taking care of other day-to-day IT priorities.
Due to yearly maintenance costs and the need for redundancy, these companies were essentially paying for the equivalent of two ERP systems over the typical five to seven-year lifespan of an on-premise system.
Today, companies (e.g., pharmaceutical firms) generally choose an on-premise solution for compliance or customization reasons. In the latter case, the companies foresee an ROI from customizing the programming of the ERP system to meet their special needs.
Cloud-based ERP software
In contrast to on-premise software, a cloud-based ERP system (informally known as “cloud ERP”) runs in the cloud as opposed to company-owned servers. The cloud refers to off-site servers owned by a third-party offering a variety of IT services.
You pay for cloud ERP just as you would a magazine subscription: a monthly fee covers hosting, licensing, and a service contract. Prices will vary depending on the number of users and the functions you need to access.
Cloud ERP does not require the significant upfront investment of an on-premise solution. This dramatically lower barrier to entry has been highly advantageous for small and medium-sized businesses that want to take advantage of the following:
Very low hardware and software costs. You use the IT infrastructure you already have. You may need to purchase tablets to give your people in production mobile access to the ERP.
No-worry maintenance and upgrades. Maintenance, update management, security, and data back-up and recovery are all taken care of by the provider. So your IT team is free to deliver value on other projects.
Remote access to your ERP at any time. A cloud-based solution means your salespeople, technicians, and delivery staff on the road as well as your team working remotely enjoy anytime-anywhere access to your ERP system.
Pre-installed training software. Top-tier cloud ERPs include easy-to-use training modules in their ERP solution.
Enterprise-grade cybersecurity. Major cloud service providers offer a level of security and compliance that is beyond what most smaller businesses can afford.
What ERP implementation costs should I account for?
Integrating your new enterprise software into the company’s way of doing business is a critical phase in your digital transformation. Let’s cost the ERP implementation based on three key stages.
1. Migrate the legacy data
Before you migrate data to the new system, you’ll need an expert to analyze your current processes and how they will “translate” to the new system. This analysis may reveal that either you have to re-engineer the process to accommodate the new ERP or you need to customize the software. Both the process audit and the customizations need to be costed.
Due to the high stakes of data migration, senior managers must take ownership of the data transfer for their respective business functions. Thus, production leaders need to oversee the migration of their production data, and so on. The time invested by the leadership needs to be estimated and included in your TCO.
2. Test the new ERP system
The integrity of the data must be tested at every level of your processes. After the migration, retest the data. Expect the unexpected!
Naturally, you’ll need to account for these precautionary measures.
3. Decommission of the legacy system
When you flip the “off” switch on your legacy system, you need to block access to any new data input, and take the steps necessary to remove the old software. Include these costs in your TCO calculator.
To maintain an accurate TCO, it’s important that you be clear on how much support your provider can offer. Some questions you may want to ask them:
- What part of the implementation process will they handle?
- How will bridges to other software and customizations be invoiced?
- What kind of support do they offer after deployment (webinars, documentation, phone support)?
As you’re costing these three stages, do not assume the sunniest implementation scenario. Leave room in your costing for unforeseen events.
Throughout the ERP implementation, all members of your team need to be cost-aware, all the time. If people lose focus on the ERP vision articulated in the list of requirements, the project risks brutal cost overruns and even failure.
What are the hidden costs of day-to-day use of the IT infrastructure?
Just like the other equipment in your plant, IT infrastructure incurs on-going costs. These must be accounted for in your ERP’s TCO. The following table highlights the differences in these costs for cloud and on-premise ERPs.

What are the ERP’s hidden day-to-day costs on the workforce?
During the ERP implementation, company productivity will take a hit in hidden ways.
For example, your ERP project team will, or should, involve your best people. They will have to devote a part of their workweek to the project. That includes the senior executive who is the project lead. As a result, these employees either will have to put some of their daily tasks on hold or hire help to pitch in.
What’s more, your legacy system will be offline as the new system is being worked on. Meanwhile, you’ll be paying wages as usual and having to closely manage your customers’ expectations while not being at full capacity.
There are other people costs to include in your TCO. Think of the employees who may resist the system change and leave. You’ll have to recruit and train new ones.
Training will be an on-going cost because your ERP is only as good as the trained people who use it. Even after your people master the basics, they’ll need further training down the line as your growth obliges them to exploit more capabilities of the ERP system.
To support you along your ERP journey, you’ll need to hire the professional services of consultants and change management experts, among others. To cost for these services, speak to your potential vendors regarding the expertise required for your project.
To learn more about the costs of a cloud ERP system, read our post, “Is Cloud ERP a Cost or an Investment? Building the Business Case for Investment”
The upside of your ERP TCO calculation
While compiling the various obvious and hidden costs of your TCO, you may find the accumulating costs disheartening. To keep these costs in the right perspective, we recommend you calculate these two situations:
- The cost to your business of not investing in an ERP ? in other words, of doing nothing
- The productivity and agility benefits that a well-implemented ERP will return to you on an on-going basis.
Through the latter calculation, you’ll see how your business will do the following:
- Reduce manual labour and errors
- Automate and streamline non-value-adding processes and enhance operational efficiencies
- Improve your production and financial forecasting for more efficient operational and financial management
- Help you use your equipment in a more economical way that prolongs its lifespan
- Benefit from real-time 360-degree visibility into your operations so you can make more proactive decisions faster.
As a result of these benefits, your teams will have more time to:
- Work with, and sell to, customers
- Develop or finetune products and processes
- Pursue new opportunities for growth.
You’ll be very glad you crunched the numbers.
If you have more questions, do reach out to us.