To run your business sustainably, information is vital.
And not just any information. It must be reliably right, and available at the right time.
When your information strays from these parameters - when it’s less accurate, less timely - you increase the risk and cost of your data-supported decisions. In a growing business, where a fast-increasing number of components is moving to different locations, the consequences of these decisions increase accordingly.
Yet, many small and medium-size enterprises still make do with information that is neither accurate nor timely.
In fact, getting reliable data from operations in a timely fashion is one of the key challenges of many SMEs, in the food and beverage sector as well as others.
Let’s look at why this is so.
What typically happens to information on its route through an SME
In many SMEs, information traveling through an organization may suffer the fate of mishandled airline luggage: it may get delayed, battered by error, and even sidetracked in a silo. For example, consider the way raw materials are accounted for upon arrival at the trucking dock of a typical SME.
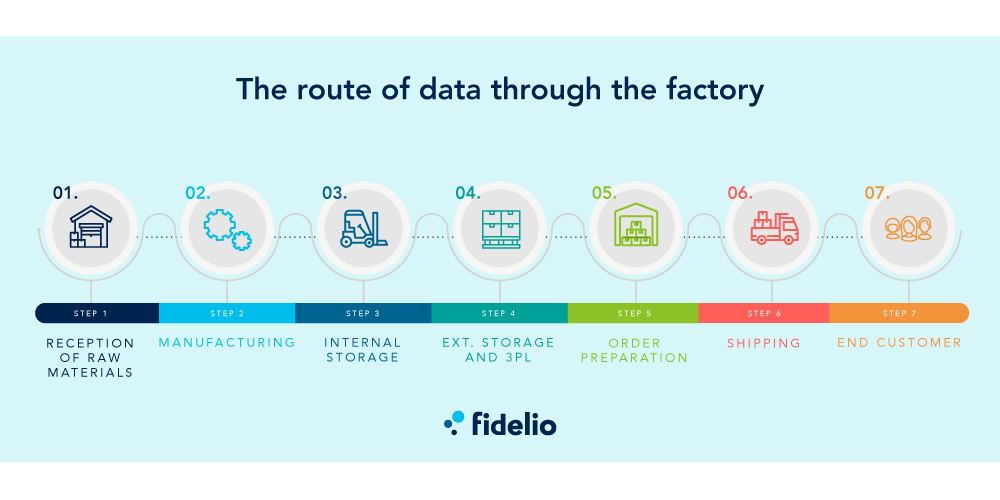
fter a time-consuming manual count of the goods, the receiving clerks sign-off, if all is good, on the paper-based receiving documents. Let’s say 10 units of X are received.
Often, these 10 units are not entered into inventory by the receiver but by an administrative clerk in another department, hours or days later. During this lag in data entry, any inventory reports consulted or created will be inaccurate. Hopefully, your production manager will not be in dire need of X in the interim.
The data gets more inaccurate
But let’s say this manager does need X to fulfill an order. Through good luck, he or she spots the freshly-arrived X and puts five units into production. This usage may be documented on paper, a spreadsheet, or software residing in a computer that does not communicate with any other department.
At this point, who in the company knows exactly how much X is on hand? No one, unless a physical count is carried out on the spot.
The quantity of X in inventory gets even foggier. After production of the order with the X component and shipment of the finished goods, when does invoicing take place to account for all the new changes in inventory? A day or days later?
Imagine now the plight of the production manager planning production for incoming orders. He or she may request a physical count or consult an inventory status report.
This report is produced regularly after all departments have presumably met their accounting count-offs by manually entering multiple times the same data (with who knows how many errors “polluting” the data).
Traceability adds to the challenge of inventory tracking
What adds another degree of difficulty to inventory control in the food and beverage sector is the compliance-driven requirement to trace all the components of production.
This requirement makes It essential to assign a lot number at the right time to all components and to record in a timely way the sourcing details of the lot in a ledger. Should an audit or recall be required, the business needs to have the data quickly available.
Good data practices and tools to put in place
Given this fog of data inaccuracy and all the risks and costs it brings on, it’s understandable that a management team would want tighter control over the quality and speed of data reporting. To achieve this goal, business leaders can do the following:
- Staff the data-entry team adequately so that it can process the volume of work satisfactorily. (Recruitment may be challenging and costly during the current labor shortage.)
- Create an ergonomically healthy environment for the employees carrying out these repetitive, meticulous tasks.
- Train employees on correct data-entry and double-checking practices, and insist on rigorously respected cut-offs.
- Set attainable accuracy goals.
- Identify and address sources of data inaccuracy.
- Keep a register of lot numbers.
These sound data practices will support better data accuracy and more timely reporting. Yet, these practices do not address other sources of inadequate data reporting.
For example, enhanced data entry does not eliminate the problem of the data residing in software programs that do not communicate with each other. When business information is siloed like this, report creation requires somebody to coordinate data collection from the various sources.
Furthermore, your visibility into your operations is limited by the capacity of each software program for data analysis. For example, will your accounting program allow you to drill down into finished goods costs to analyze the component costs and their sources?
As your business grows, you’ll have to keep adding data-entry staff to keep up with the increasing volume of data. These wages do not add value to your bottom line.
Fortunately, you don’t have to work this way.
An Enterprise Resource Planning (ERP) system eliminates these data-related vulnerabilities and offers you real-time 360-degree visibility into your operation. Here are the top five ways an ERP system works with real-time data to help you reduce risk and cost in your SME.
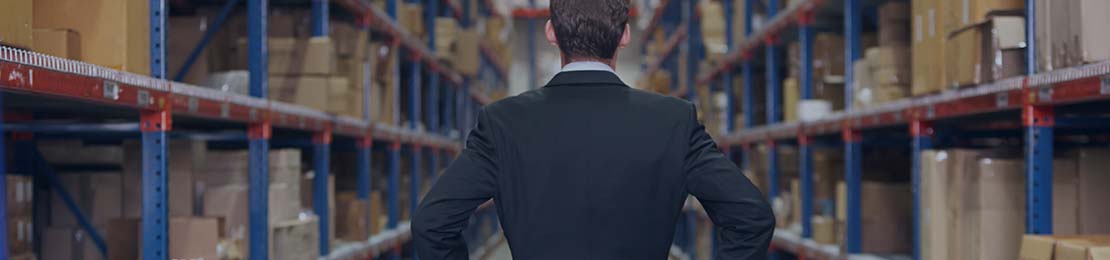
1. Your ERP minimizes data entry
Your ERP system unifies all of the data of each of your business functions and centralizes it in one database, which is updated in real time whenever new data is entered.
For example, when you ship 10 units of X, those units are automatically deducted from inventory, the customer is invoiced, and a notification for a follow-up call is sent to customer service ?? all done in the blink of an eye. This automation alone removes several steps of repetitive, potentially erroneous data entry.
2. Tracks everything and forecasts better
Once an item of value is entered into your ERP system, you can track its history as it moves from your reception dock to your end-customer’s door. This real-time visibility into the physical flow of all your materials and stock enables your manufacturing team to be much more efficient and precise in their production and planning.
For example, the ERP system translates customer orders into the necessary requirements in materials, labour, and equipment time. With this real-time snapshot of how your manufacturing operates, you empower your managers to plan future production with greater precision and efficiency.
3. Enhances your business decisions
Because the ERP integrates the data of all your business functions in real-time, your system’s reporting function can help you monitor your Key Performance Indicators (KPIs) with a glance at a dashboard. What’s more, if you need more granular detail, the ERP’s dynamic views enable you to drill down into the elements that make up the big-picture numbers.
This real-time reporting enables your leadership to take the pulse of your company’s efficiency, costs, and performance in any business function. Armed with this real-time insight into your operations, you can proactively respond to minimize emerging problems and take advantage of opportunities.
4. Empowers your team to automate more processes
Once your business is working with real-time ERP data, you open the door to additional tools that can build on this capacity to further accelerate or automate your processes. For example, if you have the necessary business volume, you may want to consider equipping your team with the following tools:
Mobile readers. When connected to an inventory system, these RFID-based devices read barcodes on incoming or outgoing products. Such scanning eliminates a lot of data entry and thus reduces the risk of error.
Tablets. Your team on the production floor can use tablets to facilitate data entry and consultation. Easy and accessible data-entry options for your staff will help build up your capacity to manage your business in real time.
EDI. Electronic Data Interchange makes it possible to retrieve data transmitted by suppliers as soon as a raw material enters the factory. For food and beverage processors, EDI data gives you a quick head start on maintaining traceability, and is significantly more efficient than working with the Excel files some vendors send.
3PL partner. With an ERP system, it’s easy to track inventory stored at a business partner's warehouse and provide their team with shipping instructions.
Connection to the IoT (Internet of Things). Once sensors and communication capacity are installed on your machinery, your equipment will be able to communicate directly with your ERP system and other helpful parties. For example, a properly equipped weight scale can automatically gauge the weight of an object and communicate it directly to your ERP system — no one needs to enter the data.
5. Enhances business intelligence
The ERP data your business generates can be overwhelming to analyze without help. Fortunately, the right ERP systems enable you to take advantage of analytics tools which transform data into information you can interpret and act on.
These sophisticated analytics functions used to be expensive and reserved for big enterprises, but advances in technology have now made them accessible to SMEs and a standard feature on some ERP systems.
Basically, analytics functions carry out a data-mining function. In other words, they review large collections of data to discern patterns and trends based on the user’s query. You could answer questions such as:
- Which markets are the greatest source of profitable sales?
- Which aspect of your production chain is the most efficient?
- Which suppliers provide the highest quality materials?
- What trends are there in your equipment breakdowns/downtime?
- When are customer returns at their highest and which product categories are the most impacted?
As you manage the challenges of growth, you need reliable and timely information to support your decision-making and reduce risk and cost. Real-time ERP data is the ideal solution for these challenges.
For more information on how real-time data can work for you, contact Fidelio today!